1、cnc precision machining parts basic overview
1.1 – Definition and principles of CNC machining
CNC, or Computer Numerical Control, is a technology that uses digital programs to control machine tool movements and machining processes. In CNC machining, the operator first creates a three-dimensional model of the part from its design drawings using computer-aided design (CAD) software. Subsequently, with the help of computer-aided manufacturing (CAM) software, the 3D model is converted into CNC programs, such as G-codes, that are recognized by the machine tool. These programs precisely specify the machine’s trajectory, speed, depth of cut and other parameters. According to the received CNC program, the machine tool precisely controls the relative motion between the tool and the workpiece through the motor-driven ball screw and other transmission devices, thus realizing various machining operations such as cutting, drilling, milling, boring, etc. on the workpiece, and accurately machining the raw material into the desired shape of the part.
1.2 – Development history of CNC machining
CNC machining technology originated in the mid-20th century. In the early days, CNC technology was mainly used in the military field for manufacturing high-precision weapon parts. With the rapid development of electronic technology and computer technology, CNC machining technology has gradually matured and is widely used in civilian manufacturing. From the initial simple CNC system, can only carry out the basic linear and circular interpolation movement, to today’s advanced multi-axis linkage CNC system, can realize extremely complex surface processing, CNC machining technology continues to breakthrough innovation. Today, CNC machining has become one of the core technologies of modern manufacturing, greatly promoting the automation and intelligent development of manufacturing.
1.3 – Types and characteristics of CNC machining equipment
1 – Machining center
Machining center is one of the most common CNC machining equipment with tool magazine and automatic tool changer. It is able to complete a variety of processes in a single clamping, such as milling, drilling, boring, tapping, etc., which significantly improves the machining efficiency and accuracy. Machining centers can be divided into vertical machining centers and horizontal machining centers. Vertical machining centers are suitable for machining height direction of small size, complex plane contour parts; horizontal machining centers are more suitable for machining box class and other parts that require multi-face machining, which has the advantage of machining accuracy and stability.
2 – CNC lathes
CNC lathe is mainly used for the machining of rotary parts, such as shafts and disk parts. By controlling the movement of the tool along the X-axis and Z-axis through the CNC system, it can accurately turn a variety of rotary surfaces such as external circle, internal hole, thread, taper, etc. The CNC lathe is characterized by high machining accuracy, high productivity and high automation. CNC lathe is characterized by high machining precision, high productivity and high automation, especially suitable for mass production of rotary parts.
CNC milling machine can carry out plane milling, contour milling, cavity milling and other processing of the workpiece. The main difference between it and the machining center is that there is no automatic tool changer, and the tool needs to be changed manually during the machining process. CNC milling machine structure is relatively simple, low cost, suitable for processing some of the parts that do not require a high degree of process concentration.
4 – EDM machine tools
EDM machine tools utilize the principle of discharge corrosion to process workpieces. When a pulse voltage is applied between the tool electrode and the workpiece, a discharge channel is formed in the narrow gap between the poles, generating an instantaneous high temperature, which makes the workpiece material locally melt or even vaporize, thus realizing the etching processing of the workpiece. EDM is suitable for processing conductive materials with high hardness and high melting point, as well as some parts with complex shapes that are difficult to be processed by traditional cutting methods, such as cavities of molds and fine shaped holes.
5 – Wire-cut processing machines
Wire EDM machine tools also utilize the principle of electrical discharge corrosion to cut and process workpieces using a moving wire as the tool electrode. According to the running speed of the electrode wire, it can be categorized into fast walking wire cutting and slow walking wire cutting. Fast-feeding wire cutting speed, low cost, but the processing precision is relatively low; slow-feeding wire cutting processing precision, good surface quality, can be used for processing precision molds, fine parts and so on.
2、The advantages of CNC precision machining parts
2.1 – High precision and stability
CNC machining can achieve very high machining accuracy, generally can reach ±0.01mm or even higher, some advanced equipment can control the machining accuracy of ±0.001mm, which is due to its accurate CNC system and precision transmission device, can be strictly in accordance with the programming instructions to carry out machining operations, to avoid the error caused by human factors. In mass production, CNC machining can ensure that the dimensional accuracy and quality of each part is highly consistent, the stability and reliability of the product has been greatly improved. For example, in the aerospace field, engine blades and other key components require high precision, CNC machining can ensure the shape precision and surface quality of the blade to meet the performance requirements of the engine in high temperature, high pressure, high speed and other extreme working conditions.
2.2 – Ability to machine complex shapes
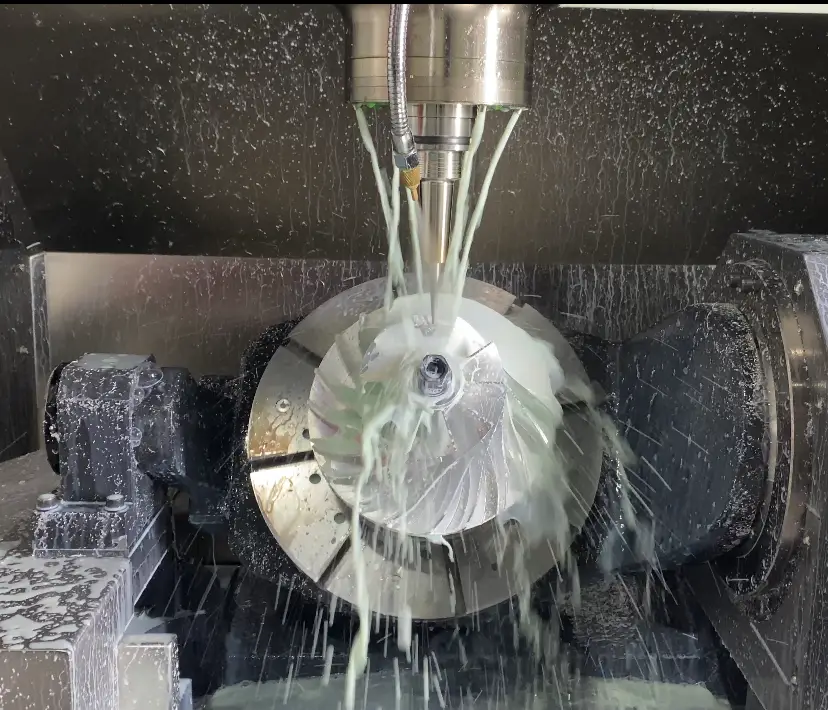
CNC machining has a strong ability to machine complex shapes, especially through multi-axis linkage technology. While traditional machining methods often face difficulties in machining complex curved surfaces and shaped structures, CNC machining centers are able to cut complex shapes with ease through 3-axis, 4-axis and even 5-axis linkage, where the tool can machine the workpiece from multiple angles. For example, the intake manifold of an automobile engine has complex internal runners that require precise control of gas flow to improve engine performance, and CNC machining is able to accurately machine them. In the medical device field, customized implants, such as hip and knee replacements, need to be precisely matched to the human bone structure, and CNC machining’s ability to machine complex shapes meets this need and ensures that the implants are well adapted and biocompatible.
2.3 – Efficient production
CNC machining equipment typically has high cutting and feed speeds, enabling rapid removal of workpiece material. At the same time, their ability to perform multiple processes in a single clamping reduces the number of workpiece clamping and auxiliary time, greatly improving productivity. In mass production, CNC machining equipment can run 24 hours a day, through the automated production process, can quickly complete a large number of parts processing tasks. For example, in the electronic equipment manufacturing industry, cell phone shells, computer heat sinks and other parts of the production, the use of CNC machining can achieve efficient and rapid mass production to meet the market demand for a large number of products.
2.4 – Wide range of material adaptability
CNC machining can be adapted to the machining of a variety of materials, including metal materials such as aluminium alloy, stainless steel, titanium alloy, copper alloy, etc., as well as non-metallic materials such as plastics, nylon, acrylic, wood and so on. Different materials have different physical and chemical properties, CNC machining through the selection of appropriate tools, cutting parameters and machining processes, can be effectively processed under the premise of ensuring the quality of processing a variety of materials. For example, in the aerospace field, titanium alloy is widely used in the manufacture of aircraft structural components and engine parts due to its high strength, low density, high temperature resistance and other excellent properties.
2.5 – Product Consistency and Repeatability
Once the CNC machining program is written and confirmed by debugging, in the subsequent production process, the machine tool will be strictly in accordance with the program for processing, no matter how many parts are produced, can ensure that the dimensional accuracy, shape accuracy and surface quality of the parts are highly consistent. This product consistency and repeatability in mass production is of great significance to ensure product quality stability, reduce scrap rate, improve production efficiency and economic benefits. For example, in the manufacture of automotive parts, engine block, transmission gears and other key components need to be mass-produced, CNC machining product consistency and repeatability can ensure the quality of these parts in different batches of production stability, so as to ensure the overall performance and reliability of the car.
3、Examples of precision CNC machined parts in different industries
Engine parts
- Cylinder block: Cylinder block is one of the core components of the engine, its internal structure is complex, there are a number of cylinder bores, water jackets, oil passages, etc. CNC machining can accurately ensure the cylindricity and roundness of the cylinder bores, as well as the positional accuracy of the bores, to ensure a good sealing of the engine and the power output. For example, in the machining of aluminum alloy cylinder block, through the high-speed milling and precision boring process of CNC machining center, it can efficiently remove the excess material and ensure the machining precision, so that the performance of the engine has been improved, and reduce its own weight and improve the fuel economy.
- Crankshaft: The crankshaft is a key part of the engine which is responsible for converting the reciprocating linear motion of the piston into rotary motion, its shape is complicated, and the requirements for dynamic balance and machining accuracy of the journal are extremely high. the use of CNC numerical control lathe and grinder can accurately process the main shaft journal, connecting rod journal, and the transition fillet of the crankshaft, to ensure that the dimensional accuracy, cylindricity, and surface roughness of all the journals, and to meet the requirements of smoothness and reliability of the engine during high speed rotation. The dimensional accuracy, cylindricity and surface roughness of each journal are ensured to meet the requirements of smoothness and reliability of the engine during high-speed rotation.
Chassis components
- Steering Knuckle: The steering knuckle connects the wheels with the suspension system, and bears complex loads in the process of automobile driving.CNC machining can accurately process the steering knuckle’s mounting holes, articulation surfaces, and other parts, to ensure the dimensional accuracy and shape tolerance, so that the steering knuckle can be more accurately coordinated with other parts, thus improving the automobile’s maneuvering performance and driving safety.
- Wheel Hub: As an important part of the wheel, the wheel hub not only needs to have sufficient strength, but also has high requirements for appearance and dynamic balance performance. Through CNC machining, rims, spokes and other parts of the wheel hub can be accurately machined to realize lightweight design and ensure its structural strength. In the process of machining, CNC programming can also be used to achieve a variety of appearance design to meet the personalized needs of different consumers on the appearance of the car. At the same time, CNC machining can ensure the dynamic balancing precision of the wheel hub, reduce the vibration of the car during driving, and improve driving comfort.
1. Aircraft structural components
- Wing Beam: The wing beam is the main load-bearing structural member of an aircraft wing, and is usually made of high-strength aluminum alloy or titanium alloy. Due to its large size and complex shape, the strength-to-weight ratio is extremely high, and CNC machining technology plays an important role. Through the large CNC gantry machining center, the raw material can be efficiently cut and processed, and the external dimensions, thickness and internal structure of the wing beam can be precisely controlled, so as to minimize the weight and improve the fuel efficiency and flight performance of the aircraft under the premise of ensuring the structural strength.
- Fuselage frame: the fuselage frame consists of numerous profiles and connectors, and its machining accuracy directly affects the assembly quality and overall performance of the aircraft. cnc machining can accurately machine the various parts of the fuselage frame, ensure the precision of the fit between the parts, reduce the assembly error, and improve the structural integrity and reliability of the aircraft. In the machining process, suitable tool paths and cutting parameters are adopted for different materials and part shapes to ensure machining quality and efficiency.
2. Engine parts
- Turbine blades: Turbine blades are one of the harshest components in an aero-engine and need to work for a long time under high temperature, high pressure and high speed. Therefore, turbine blades are usually made of high-performance materials such as nickel-based high-temperature alloys and have complex aerodynamic shapes. 5-axis CNC machining can accurately machine the blade shape, tenon, and internal cooling channels of the turbine blades to ensure the accuracy and surface quality of the blades and improve the thermal efficiency and thrust of the engine.
- Engine casing: As the casing of the engine, the engine casing needs to withstand great pressure and vibration, CNC machining can accurately process the mounting holes, sealing surfaces and other parts of the casing, to ensure that the dimensional accuracy and shape tolerance of the casing, to ensure a close fit between the engine components, and to improve the reliability and safety of the engine.
Medical Device Industry
implant
- Hip Replacement: Hip replacement surgery is a common treatment for hip diseases, and the hip replacement needs to be precisely matched to the human skeleton to ensure good biocompatibility and long-term stability.CNC machining can accurately manufacture personalized hip replacements, including acetabular cups, femoral stems and other components, according to the patient’s skeleton data using titanium alloys and other biocompatible materials, and its high-precision machining can ensure a close fit between the replacement and the skeleton to reduce postoperative complications and improve patients’ quality of life. The high precision of CNC machining ensures a close fit between the replacement and the bone, reduces postoperative complications and improves the patient’s quality of life.
- Spinal internal fixator: Spinal internal fixator is used to treat spinal fracture, scoliosis and other diseases, which requires very high dimensional accuracy and mechanical properties. cnc machining can accurately process all parts of the spinal internal fixator, such as screws, rods, etc., to ensure the accuracy of the threads, the tolerance of the diameter, and the quality of the surface, so as to enable it to reliably play the role of fixation and support in the body, and to promote the rehabilitation of the spine.
surgical instruments
- Laparoscopic instruments: Laparoscopic surgery has the advantages of less trauma and faster recovery, and has been widely used in the clinic. Laparoscopic instruments, such as surgical forceps, scissors, etc., need to have fine operating performance and good biocompatibility.CNC machining can accurately manufacture the components of laparoscopic instruments, to ensure their dimensional accuracy and surface roughness, so as to make the opening and closing of the instruments, clamping and other actions more flexible and accurate, and at the same time to ensure that the surface of the instruments is smooth, reducing the damage of the human body tissues.
- Dental Surgical Instruments: Dental surgical instruments, such as dental drills, root canal instruments, etc., require a high degree of precision and sharpness, and CNC machining is able to use special cutting tools and processes to accurately machine the cutting edges and working parts of dental surgical instruments to ensure their sharpness and durability, and to provide reliable tooling support for the smooth conduct of dental surgery.
Mobile phone parts
- Mobile Phone Shell: With the increasing demands of consumers on the appearance and texture of cell phones, the design and manufacture of cell phone shells are becoming more and more complex.CNC machining can use aluminum alloy, stainless steel and other materials to accurately process various shapes and details of cell phone shells, such as chamfered edges of bezels and grooves of buttons, etc., and at the same time, ensure the dimensional accuracy and surface quality of the shells, so as to make them have a good sense of touch and appearance effects. During the processing, the surface treatment process such as anodizing and sandblasting can also be used to further enhance the corrosion resistance and decorative properties of the cell phone shell.
- Internal structural parts of cell phone: The internal structural parts of cell phone, such as the motherboard bracket, battery bracket, etc., although small in size, but require high precision, CNC machining can accurately manufacture these structural parts to ensure the precision of their coordination with other parts, to ensure that the cell phone internal parts of the installation of a solid, to improve the overall performance and reliability of the cell phone.
Computer parts and components
Computer radiator: the performance of computer radiator directly affects the stability and life of the computer, CNC machining can use aluminium alloy and other materials to accurately machine the fins and base of the radiator, and optimize the shape and arrangement of the fins to increase the heat dissipation area and improve the efficiency of heat dissipation. At the same time, CNC machining can ensure the assembly precision between the radiator components to ensure good heat conduction performance.
- Laptop casing: laptop casing needs to have thin, light, strong, beautiful, etc. CNC machining can use magnesium and aluminium alloy and other materials, through precision milling and stamping process, to create a complex shape of the laptop casing, while ensuring the strength and dimensional accuracy of the casing, so that it meets the needs of protecting the internal hardware, but also has a good appearance of the texture.
4、Future trends in precision CNC machined parts
Intelligent and automated development
With the continuous development of artificial intelligence, Internet of Things and other technologies, CNC machining will move further in the direction of intelligence and automation. The future CNC machining equipment will have intelligent sensing capabilities, able to real-time monitoring of various parameters in the machining process, such as tool wear, workpiece deformation, cutting force, etc., and through artificial intelligence algorithms to automatically adjust the machining parameters, optimise the machining process, improve machining quality and efficiency. At the same time, automated logistics systems, automated loading and unloading devices will be deeply integrated with CNC machining equipment to achieve unmanned production, reduce human intervention, reduce production costs, improve production efficiency and product quality stability.
High-precision and ultra-precision machining technology enhancement
- In some high-end manufacturing fields, such as aerospace, semiconductor, optics, etc., the machining precision requirements for parts will become higher and higher. In the future, CNC machining will continue to improve the level of high-precision and ultra-precision machining technology, through the development of new machine tool structures, high-precision transmission devices, advanced numerical control systems and precision measurement technology, to achieve higher machining accuracy, such as nano-level precision machining. This will provide technical support for the manufacture of more advanced products and promote the development of related industries.
Integration with technologies such as additive manufacturing
- CNC machining is converging with emerging manufacturing technologies such as additive manufacturing (3D printing). Additive manufacturing has a unique advantage in creating complex structural parts, while CNC machining excels in ensuring part accuracy and surface quality. In the future, the combination of the two technologies, first through the rapid construction of the basic shape of the part through additive manufacturing, and then use CNC machining for subsequent precision machining and surface treatment, can give full play to their respective advantages, to achieve a more efficient and flexible manufacturing process, for the innovative design of the product and rapid manufacturing to provide a new solution.
Green Manufacturing and Sustainable Development
- Against the background of increasing environmental awareness, CNC machining will pay more attention to green manufacturing and sustainable development. By optimising the machining process, reducing the use of cutting fluid and adopting green machining technologies such as dry cutting and micro-lubrication cutting, we can reduce the pollution of the environment. At the same time, reasonable selection of processing materials, improve material utilisation and reduce material waste. In addition, extending the service life of CNC machining equipment and improving the energy efficiency of the equipment are also important directions for future development.
5. Conclusion
CNC machining, as one of the core technologies of modern manufacturing, plays a vital role in many industries such as automobile manufacturing, aerospace, medical equipment, electronic equipment manufacturing, etc. with its high precision, complex shape machining capability, high productivity, wide range of material adaptability, excellent product consistency and repeatability. By analyzing examples of CNC machined parts from different industries, we can clearly see how CNC machining technology can provide strong support for product innovation and quality improvement in various industries.