1、Basic knowledge of CNC turned parts
CNC turning uses workpiece rotation as the main motion, and the tool feeds along the X and Z axes (or additional C-axis), and achieves precise cutting through the commands of the CNC system. Compared with traditional turning, it can achieve positioning accuracy of ±0.005mm and repeatability of ±0.002mm, and is capable of machining complex rotary surfaces, multiple threads and other structures. The automated tool change system and 24-hour continuous operation capability greatly enhance the efficiency of mass production, which is especially suitable for the manufacture of parts that require high accuracy and consistency.
Equipment & Tooling Systems
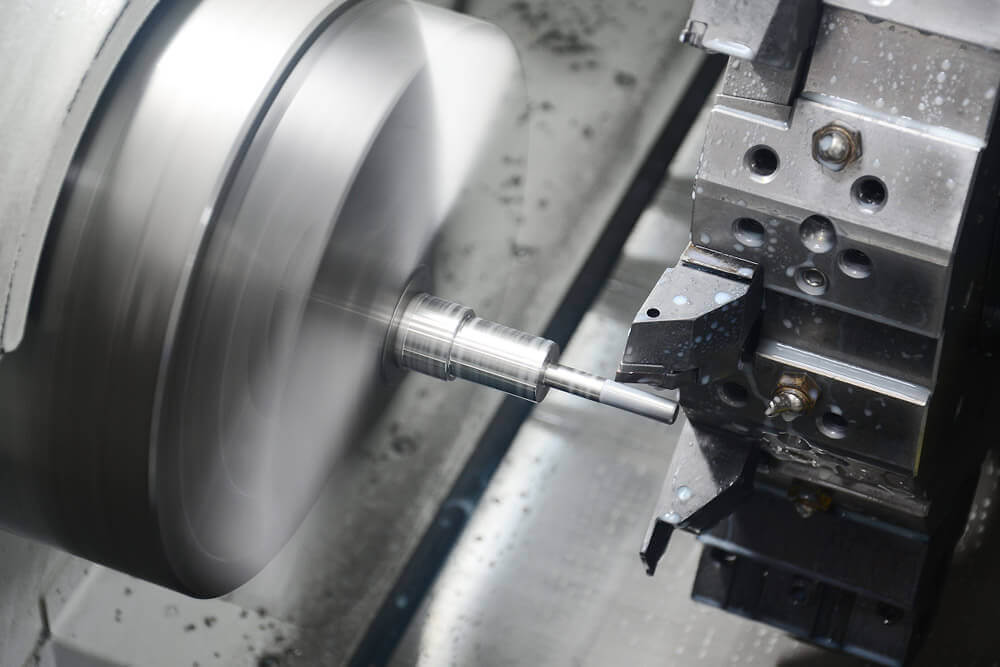
CNC lathes are classified according to their structure into horizontal (general-purpose shaft machining), vertical (high-efficiency machining of disc parts) and mill-turn (integrated milling and drilling functions). High-end models are equipped with five-axis linkage technology for non-circular cross-section machining. In terms of tooling, carbide inserts are suitable for most metal materials, ceramic tools for hardened steel (HRC55+) and PCD tools for high finish machining of non-ferrous metals. The modular turret supports 8-12 station automatic tool change to meet the needs of multi-processing.
2、Turning material selection: analysis of the characteristics of brass and aluminium
Brass CNC turned parts Characteristics
Brass (represented by H62, H80) has both good cutting and corrosion resistance, and is suitable for manufacturing valves, fittings and decorative parts. Its processing advantages are: low cutting force, not easy to stick the knife, can be used at a higher cutting speed (Vc = 120-200m/min); cutting process is stable, the chip is a short chip, easy to chip removal. However, it should be noted that high zinc content brass is prone to tool wear, and it is recommended to use coated carbide tools (e.g. TiAlN coating) and control the feed (f=0.1-0.2mm/r) to avoid deterioration of surface roughness.
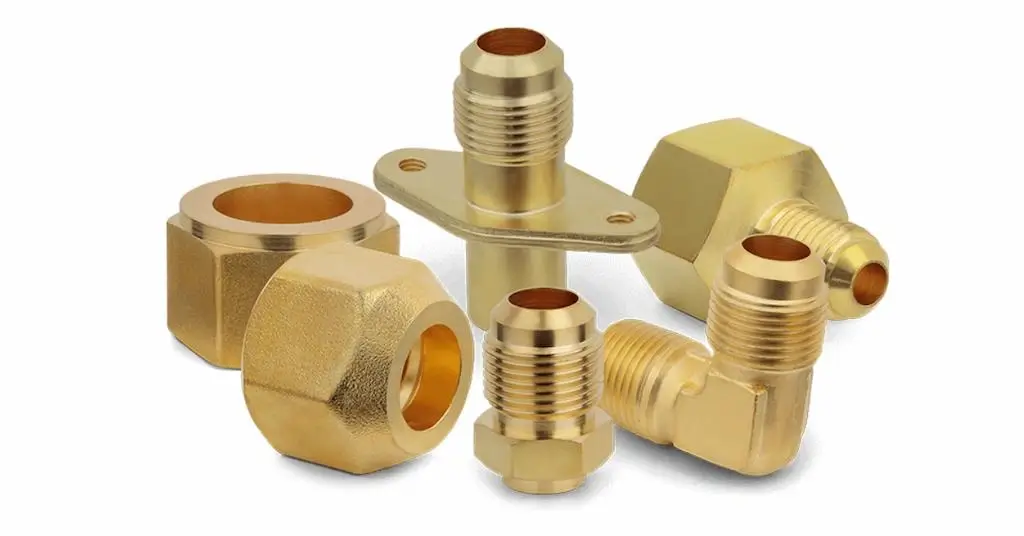
Aluminum CNC turned parts characteristics
Aluminium alloys (e.g. 6061, 7075) are widely used in aerospace and electronics due to their light weight, high strength and good thermal conductivity. When turning, it is necessary to take advantage of its low hardness characteristics and use high-speed cutting (Vc = 800-1200m/min) with a small depth of cut (ap = 0.5-2mm) to reduce the risk of deformation. For the problem of aluminium chips easily sticking to the tool, we recommend the use of PCD tools with high-pressure coolant flushing to ensure the surface finish (Ra ≤ 0.8μm). When machining thin-walled parts, the clamping method (e.g. vacuum adsorption) should be optimised to control the amount of deformation.
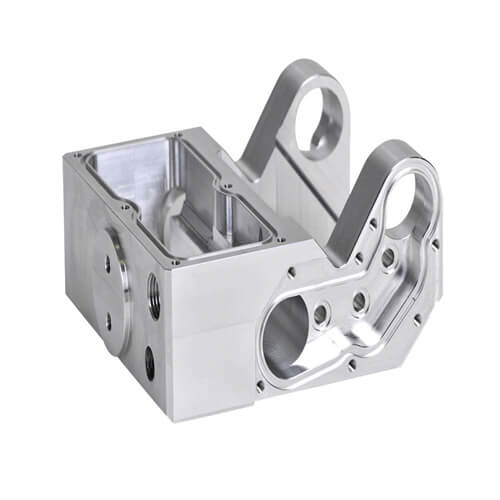
Material Selection Decision Factors
In addition to the properties of the material itself, the design requirements of the part (strength, corrosion resistance), the cost of processing (brass is about twice as expensive as aluminium), the volume of production (easy-to-cut brass for small batches, aluminium alloys for large batches) and the compatibility of subsequent surface treatments are all key considerations in the selection of materials. For example, aluminium alloys are preferred for anodised parts, while brass is suitable for parts requiring decorative plating.
3、CNC turned parts application industry depth analysis
Automotive Manufacturing
- Engine system: the crankshaft, camshaft and other key parts are turned with alloy steel, and through the process chain of roughing – semi-finishing – finishing, the roundness of the journal is controlled to be ≤0.003mm, and the roughness of the surface is Ra0.8μm. The oilway joints made of brass are precisely assembled with the cylinder block after turning, taking advantage of the oil resistance and sealing property.
- Chassis system: Aluminium alloy steering knuckle shafts are machined by mill-turn compound machining, completing the machining of outer circle, taper surface and oil hole in one clamping, with an efficiency increase of 40% and coaxiality error <0.01mm.
aerospace industry
- Engine components: Titanium alloy blade shafts need five-axis turning, with micro lubrication (MQL) technology, to control 0.002mm thin-wall deformation, surface residual stress ≤ ± 50MPa.
- Structural parts: 7075 aluminium alloy frame parts are turned at high speed and then strengthened by aging treatment to meet the needs of light weight and high strength.
Manufacture of electronic equipment
- Heat dissipation components: 6063 aluminium alloy radiator is turned to form fine fins, with anodic oxidation to enhance the efficiency of heat dissipation, surface roughness Ra ≤ 1.6μm.
- Connectors: Brass terminals are turned and plated with nickel-gold for low resistance conduction and anti-oxidation, with dimensional accuracy controlled to ±0.01mm.
Medical Device Industry
Medical titanium alloy implants (e.g. hip stems) are nano-turned to achieve a mirror finish (Ra0.1μm), combined with electrolytic polishing to eliminate machining stresses and ensure biocompatibility. Surgical instrument connectors made of brass, utilising its anti-bacterial and wear-resistant properties, are turned and passivated to meet medical grade cleanliness requirements.
CNC turned parts surface treatment applications
Protective Finish
- Anodic oxidation: Aluminium alloy turned parts are anodised with sulphuric acid to form a 10-20μm oxide film, which significantly improves corrosion and abrasion resistance and is suitable for outdoor equipment parts.
- Electroplating: brass parts plated with nickel and chromium can resist salt spray test for more than 500 hours, which is commonly used in sanitary hardware; chemical nickel plating of aluminium parts can fill the turning marks and improve the surface flatness.
Functional Surface Treatment
- Hard anodic oxidation: aerospace aluminium alloy parts are treated with hard oxidation, and the film hardness reaches HV300-500, which is suitable for wear-resistant parts such as pistons and bearings.
- PVD coatings: TiN, TiAlN coatings are deposited on the surface of turning tools, reducing the coefficient of friction by 30%, extending tool life by 2-3 times and giving the parts a decorative metallic lustre.
Surface treatment and material suitability
Brass turned parts are not suitable for anodic oxidation, but protection can be enhanced by passivation and electrophoretic coating; aluminium parts require special pre-treatment (e.g. zinc replacement) before plating to ensure bonding. The surface treatment process should be designed in conjunction with the turning process, e.g. leave 0.05-0.1mm machining allowance to avoid the coating thickness affecting the dimensional accuracy.
5、Process optimisation and quality control
Co-optimisation of cutting parameters
For the differences between brass and aluminium, the parameters need to be dynamically adjusted: brass turning focuses on tool life (Vc=150m/min, f=0.15mm/r), while aluminium turning pursues surface quality (Vc=1000m/min, f=0.08mm/r). Cutting force simulation software (e.g. Deform) was used to predict machining deformation and optimise tool paths.
Solutions to common defects
Type of problem | typical phenomenon | Brass Response Strategy | Aluminium response strategy |
surface vibration pattern | Ra value exceeded | Reduce the overhang ratio to 4:1 and use a damped toolbar. | Increase coolant pressure to 8MPa |
Size fluctuations | Diameter deviation >0.01mm | Calibration Screw Backlash Compensation | Vacuum clamping to control distortion |
Tool wear | Cutting edge chipping | Selection of fine grain carbide | Changing to PCD tools |
Intelligent quality control
Introducing online measurement system (touch probe) to detect critical dimensions in real time, and automatically correcting the tool patch when it is out of tolerance. Using AI algorithms to analyse cutting force and vibration data, predict tool life and automatically change tools to ensure that the CPK of batch parts is ≥1.33.
concluding remarks
The efficient production of CNC turned parts relies on a deep integration of material knowledge, industry experience and surface treatment technology. Brass and aluminium are typical materials, and the differences in their machining processes reflect the core logic of precision manufacturing. In the future, with the popularity of multi-axis linkage and intelligent monitoring technology, the turning process will continue to expand its boundaries in new energy vehicles, semiconductor equipment and other emerging fields. If you need to discuss specific material process parameters or industry solutions, please contact us!!!!