Liquid Silicone Rubber Molding Services
liquid silicone rubber molding is a two-component, heat-cured silicone containing a high-purity platinum salt catalyst used in the production of technical parts with high demands on strength, resistance and quality.
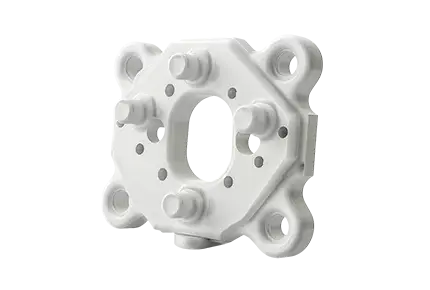
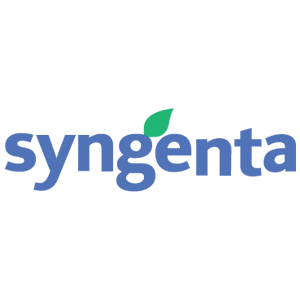
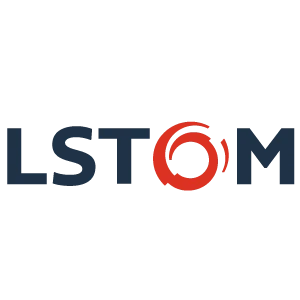
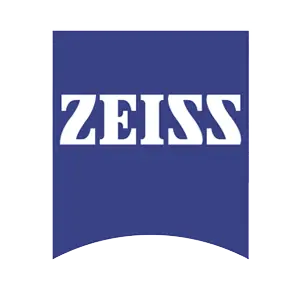
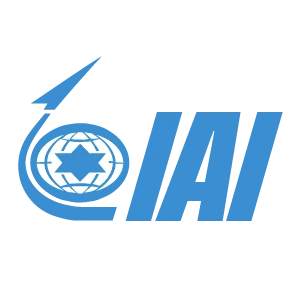
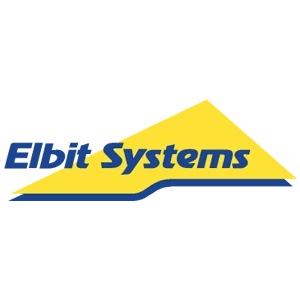
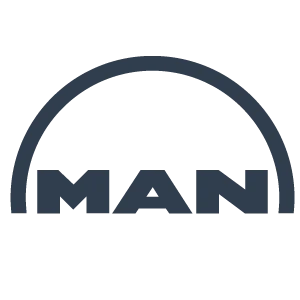
Liquid Silicone Rubber Molding Services
rapid prototyping
injection mold
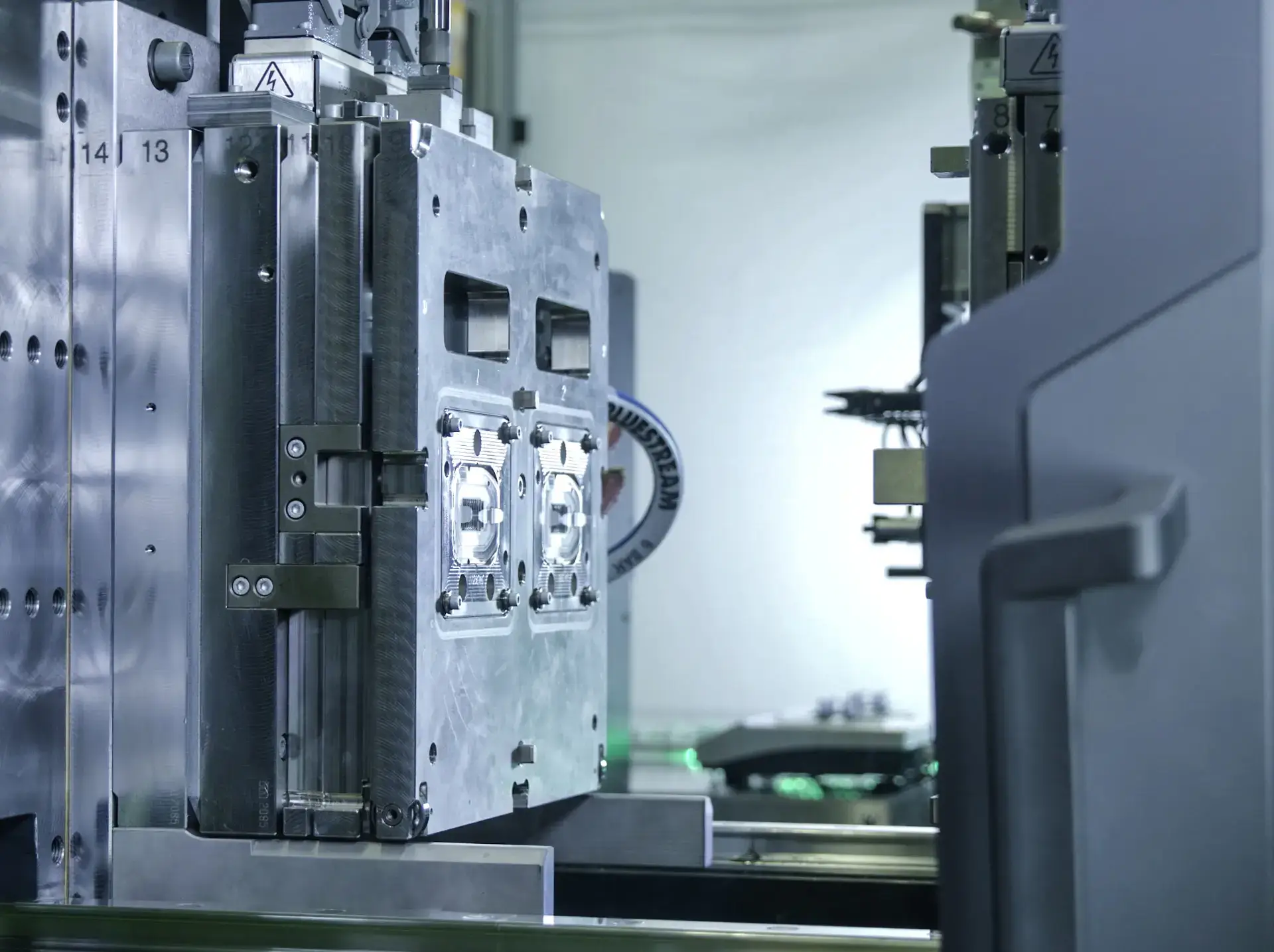
Innovative technology for the design and production of your LSR products.
We are the benchmark for liquid silicone resin parts (LSR) for OEMs.
We have the experience and technical expertise to meet a wide range of requirements in different applications.
We work hand in hand with our customers to develop quality projects and provide solutions for a wide range of needs. Whether it is a small part or a complete product, we are the ideal partner because we always offer the most professional service to guarantee excellent quality and compliance with the required delivery times.
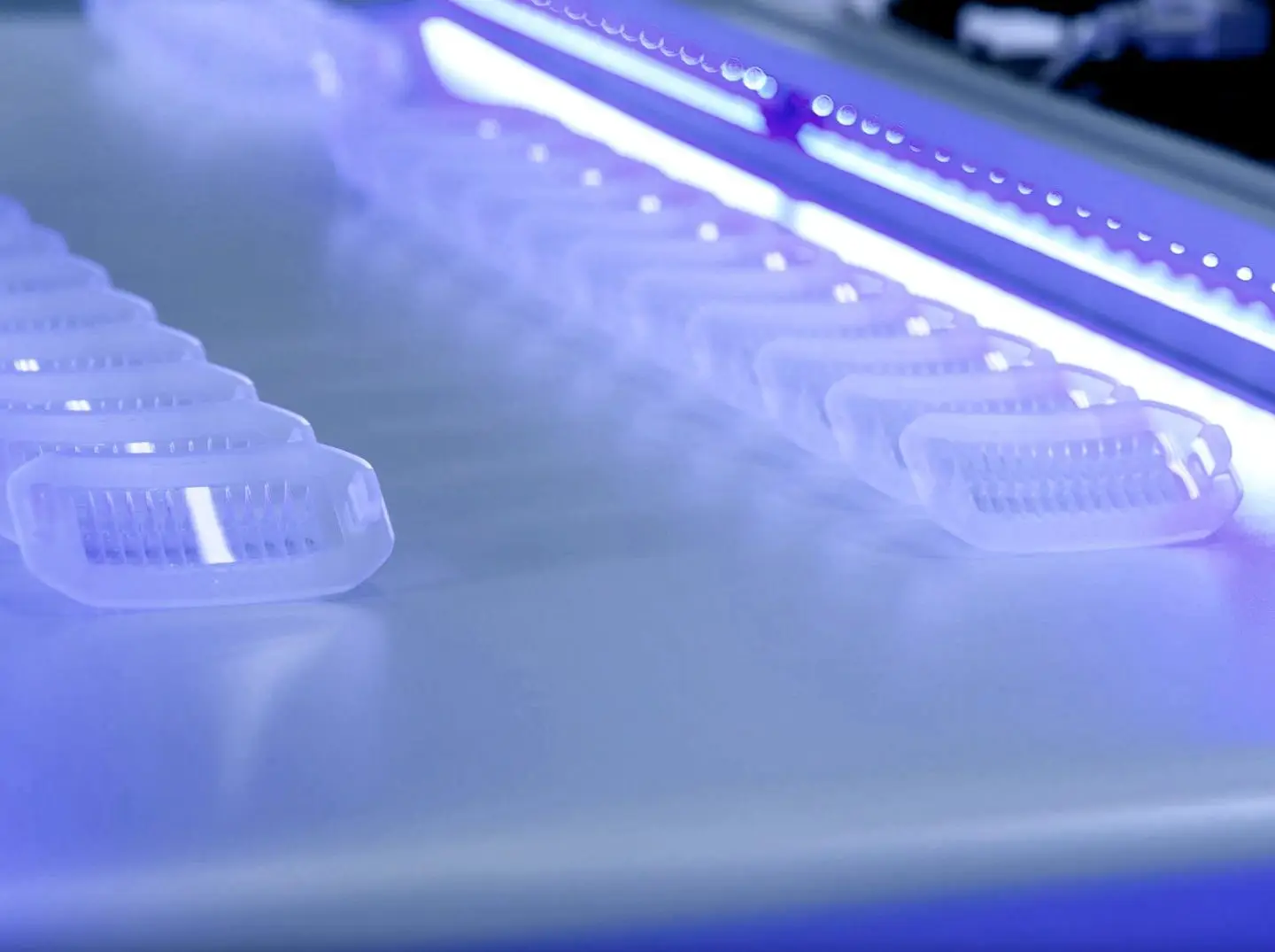
LSR: More than just a material.
Liquid silicone rubber (LSR) is a two-component, heat-cured silicone containing a high-purity platinum salt catalyst used for the production of technical parts with high requirements for strength, resistance and quality.
It is used in the production of elastic articles by means of an injection molding process. Due to the excellent physical and chemical properties of liquid silicone, this process ensures rapid injection molding of products for a wide range of applications.
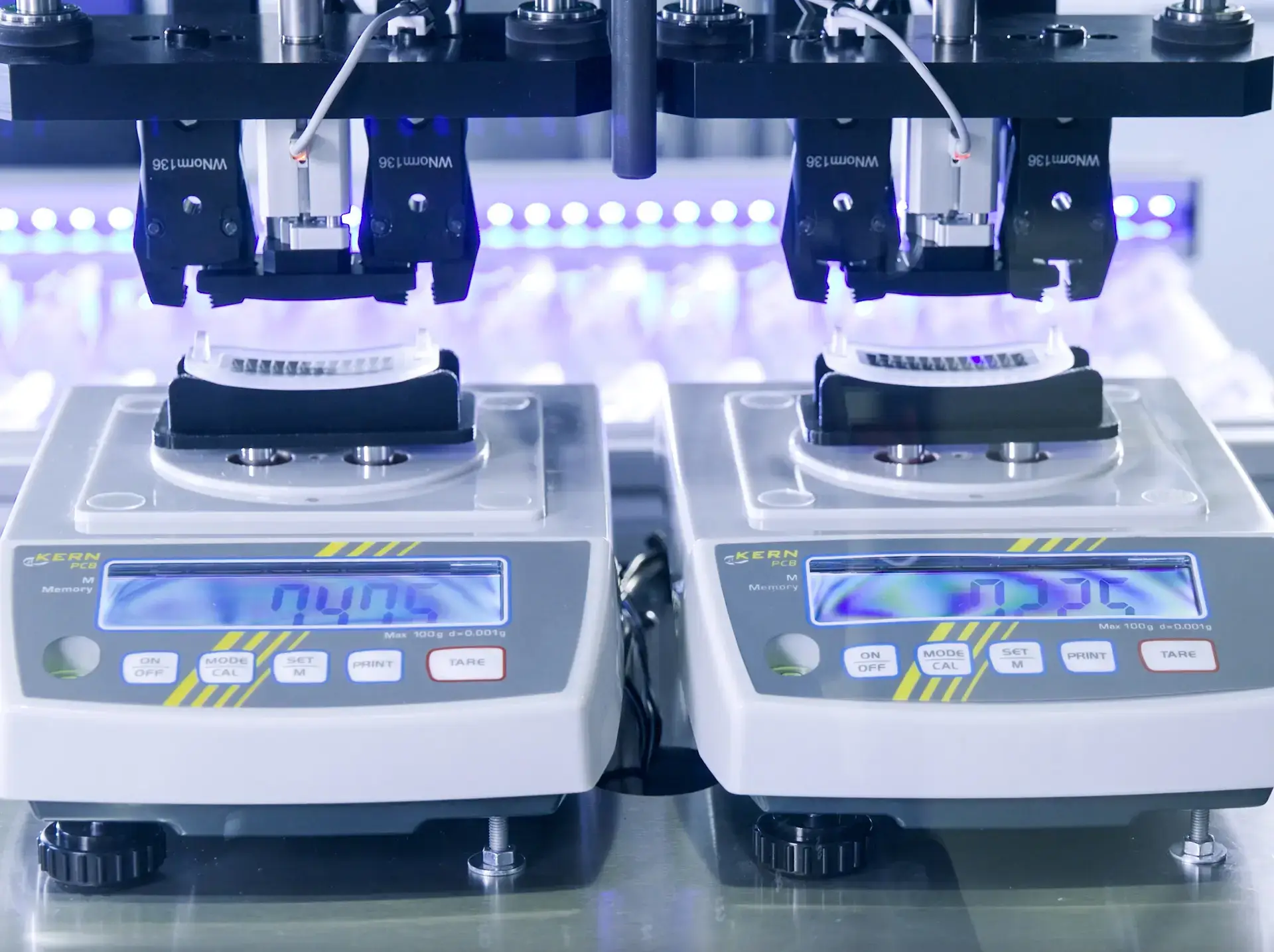
Liquid Silicone Rubber(LSR) molding
One of the most important uses of liquid silicone rubber molding is overmolding, where a rubber part is combined with a rigid part made of thermoplastic. This is particularly useful for adding shock-absorbing silicone skins to electronic devices, soft ergonomic grips to hand tools or toothbrushes, and a variety of other applications.
The process involves using a solid thermoplastic part as a substrate and then molding a silicone gel onto it. The process can be done in two ways:
Two-Color Molding: The thermoplastic is injected into the mold and allowed to cure, then the silicone gel is injected into the remaining space and allowed to cure.
Insert Molding: A preformed thermoplastic part is placed into the mold and then silicone gel is injected into the mold.
- FAQs
Frequently Asked Questions
We understand the importance of clarity and transparency in injection molding services. Below are some of the common questions we receive and detailed answers to help you make an informed decision. If you have further questions, please feel free to contact us.
Can silicone be injection molded?
Yes, silicone can be injection molded, and it’s commonly done using liquid silicone rubber (LSR). The process involves multiple components, including an injector, metering unit, supply drum, mixer, and mold clamp. LSR injection molding is widely used to produce pliable and durable parts in high volumes, ensuring consistency and efficiency in industries like medical, automotive, and electronics.
What temperature is silicone injection molding?
In silicone injection molding, the molds are typically heated to temperatures ranging from 250° to 300°F. This high-temperature range allows the LSR to cure properly, transforming from a liquid into a solid state while retaining the necessary material properties for durable, high-quality parts.
What is the process of silicone molding?
The silicone molding process involves heating the mold and injecting or compressing silicone rubber into the mold cavity. This allows the material to conform to the shape of the cavity, producing components with precise geometries. The process can be either compression molding or liquid injection molding, depending on the application and material properties required.
How much does silicone injection molding cost?
The cost of silicone injection molding can vary widely depending on the project’s complexity and size. Costs can range from $100 to over $100,000. Simple single-cavity molds may cost between $1,000 and $5,000, while complex molds can exceed $80,000. Factors like mold design, material choice, and production volume all impact the final cost.
What is the tolerance for silicone injection molding?
The standard tolerance for silicone injection molding ranges from +/-0.1mm for general parts to +/-0.025mm for high-precision components. Achieving these tight tolerances is essential to ensuring that parts meet functional, aesthetic, and assembly requirements, especially for intricate designs.
What is the pressure for silicone injection molding?
Injection pressures for molding liquid silicone rubber (LSR) vary based on the process but typically range between 200 to 1200 psi. Most applications require pressures between 300 and 700 psi to ensure proper material flow and part quality.