1、Overview of manufacturing machine parts
1 – pre-production
To carry out process preparation, confirm that the design drawings and process documents are complete, determine the machining process, process parameters, equipment, preparation and inspection of raw materials and process accessories, the development of a detailed process plan and schedule, including the determination of the processing sequence and schedule, allocation of production tasks. This link is vital to the smooth running of the subsequent production of mechanical parts.
2 – Parts Processing
Drilling, milling, turning and other cutting processes need to determine the size and shape layer by layer according to the design drawings, and finally check and polish to ensure that the size and surface quality meet the requirements.
3 – Parts assembly
Determine the assembly sequence and method in accordance with the design drawings and process documents, and carry out debugging and testing of functional performance after completion of assembly.
4 – Factory inspection
Factory inspection is the last hurdle to ensure the manufacturing quality of mechanical parts. Before the products leave the factory, the key dimensions, assembly clearance, surface quality and other comprehensive inspection, functional performance and reliability tests, complete product packaging and quality records and documentation.
2、manufacturing machine parts preparation process
1 – Confirmation of documents
Documentation confirmation is a fundamental part of mechanical parts manufacturing, ensuring accuracy and standardization of production.
Before production begins, confirm whether the design drawings and related process documents are complete. Interpret the drawings in detail, clarify key information such as part shape, size, material, etc., and understand the machining requirements and technical standards in the process documents.
2 – Determine processing details
Determine the machining process, process parameters and equipment according to the design drawings and process documents. Judge the complexity of the structure of the parts, select the appropriate machining process, such as turning, milling or grinding, and determine the cutting speed, feed, depth of cut and other process parameters to ensure machining accuracy and efficiency.
3 – Material Preparation and Inspection
Prepare raw materials and process auxiliary materials and carry out incoming inspection. Strictly control the quality of raw materials, check whether the chemical composition and physical properties meet the requirements, and ensure that the specifications and performance of process auxiliary materials meet the production needs.
4 – Pretreatment work
Pre-treatment work such as deburring, removing flying edges, cleaning, clearing and measuring are carried out on the parts to prepare them for subsequent machining. The quality of the pre-processing work directly affects the efficiency and quality of subsequent processing.
3、manufacturing machine parts process
manufacturing machine parts processing technology and methods are rich and varied, common processing technology has the following kinds:
1 – Turning processing
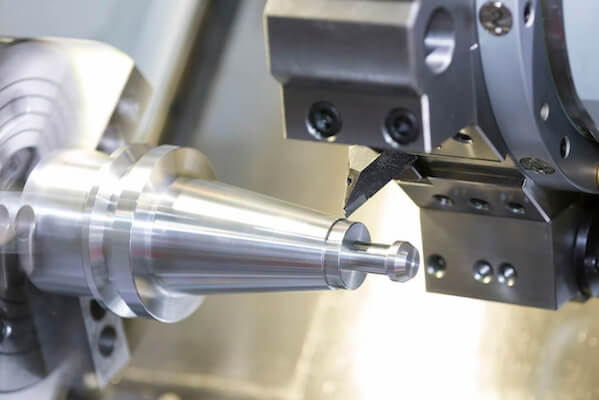
Turning is usually used for machining parts with cylindrical, conical and other rotating surfaces, such as shaft parts and disk parts. By cutting on a rotating workpiece with a turning tool, high precision machining of surfaces such as external, internal, and threads can be realized. Turning is one of the common machining methods for the production of mechanical parts.
2 – Milling Machining
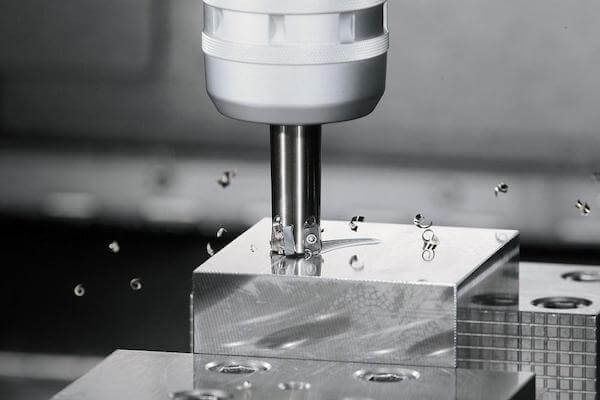
Milling is suitable for machining flat surfaces, grooves, gears and other parts. Milling machine cuts the workpiece with a rotating milling cutter, which can realize the processing of complex shapes. For example, in the production of mechanical molds, the milling process can process various shapes of cavities and convex molds.
3 – Drilling processing
Drilling is mainly used for drilling holes in workpieces with relatively high precision and surface quality requirements, and is often used to prepare for subsequent machining processes.
4 – Grinding processing
Grinding is used to improve the surface quality and accuracy of parts, such as further polishing of parts that have been turned or milled to achieve a higher surface roughness.
5 – Other processing means
In addition, there are boring, honing, polishing and other processing means to meet the special processing needs of different parts. These processing means enrich the processing methods of mechanical parts production.
4、Quality inspection in manufacturing machine parts
1 – Pre-test preparation
Adequate preparations should be made before testing, including the preparation of relevant testing equipment and tools, such as measuring instruments, testing equipment, testing tools and so on. Meanwhile, the purpose and standard of testing should be clarified in order to make accurate testing judgment.
2 – Exterior Inspection
When inspecting the appearance, the inspectors need to check the external dimensions, surface finish, wear and tear, deformation, color difference and other appearance elements according to the design drawings of the products to judge whether the products meet the requirements. For example, when inspecting the surface of mechanical parts, it is necessary to check whether there are scratches, dents, bumps and other defects, and whether the surface roughness is in accordance with the specified standards.
3 – Dimensional Inspection
Dimensional inspection is one of the important parts of mechanical parts inspection. Using calipers, vernier calipers, micrometers and other measuring tools, measure the length, diameter, depth, angle, flatness and other parameters of the parts to assess whether their dimensions meet the design requirements. Dimensional inspection is the key link to ensure the production accuracy of mechanical parts.
4 – Material Inspection
Material testing is also one of the important contents of quality testing. Through various testing methods, such as chemical analysis, tensile, compression and hardness tests, the performance of materials is tested to ensure that they meet product requirements. For example, for materials used to manufacture high-strength components, tensile tests are required to determine whether their strength meets standards.
5 – Mechanical performance testing
Mechanical performance testing is an important means of ensuring the performance of products produced from mechanical parts.
Mechanical performance testing is used to assess the product’s load-bearing capacity, stability, toughness and other properties. Through the tensile test, pressure test, bending test and other methods to ensure that product quality meets the requirements.
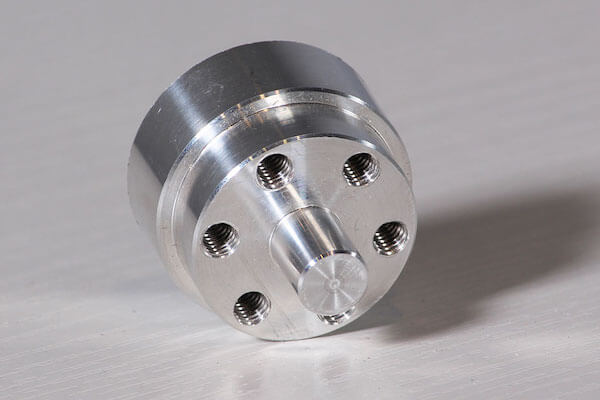
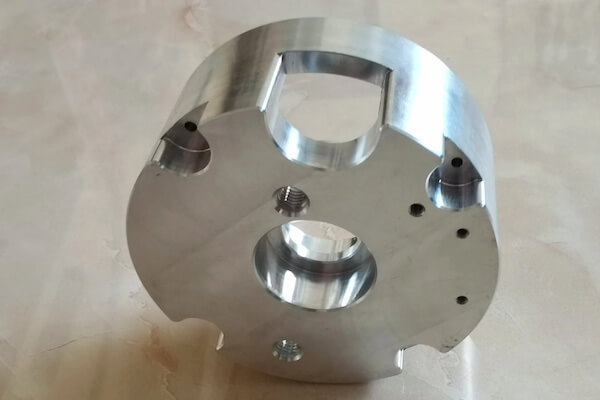
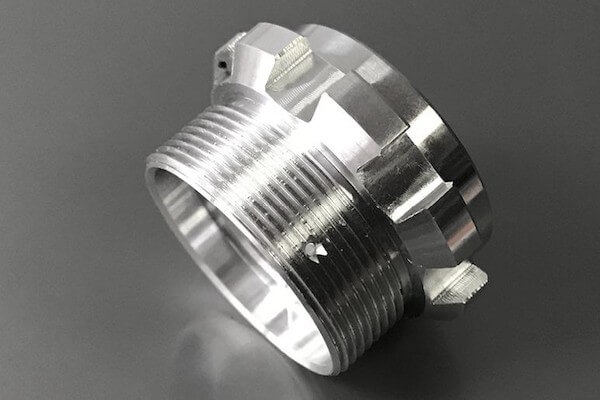
5、What should I consider when choosing a manufacturing machine parts?
1 – Processing requirements
First of all, it is necessary to clarify the processing requirements, according to product specifications and production plans, to determine the type of parts to be processed, size, accuracy level and other requirements. Such as processing high precision requirements of small parts, CNC machining centers are more appropriate choice; roughing of large parts, gantry milling machine is more appropriate.
2 – Device Functions
Subsequently, understand the functions of different types of machining equipment, including the range of machining, accuracy capabilities, and machining efficiency. For example, lathes are mainly used for machining rotating parts, milling machines are suitable for machining flat and curved surfaces, and grinding machines are used to improve the surface accuracy of parts. The function of the equipment is one of the key factors in selecting the machine parts production equipment.
3 – Selection of equipment
When selecting equipment, suitable processing equipment should be chosen according to the processing requirements and equipment functions to ensure processing quality and efficiency. At the same time, the performance, accuracy requirements, reliability, stability and other factors of the equipment should also be considered. For example, for production lines that require continuous operation for a long time, the reliability and stability of the equipment is particularly important.
4 – Price and value for money
Under the premise of meeting the processing requirements, choose the equipment with reasonable price, stable performance and easy maintenance, and also consider the long-term benefits of the equipment such as the service life of the equipment, the replacement cycle of wearing parts, and the maintenance cost. Price and cost-effective is an important consideration in the selection of machinery parts production equipment.
6、Machining characteristics of different types of manufacturing machine parts
1 – Shaft parts
Shaft parts usually have a rotary surface. In the machining process, cylindricity, coaxiality, surface roughness and other precision indicators need to be ensured. Turning process should be reasonable selection of tools and cutting dosage, in order to improve the processing efficiency and quality. Shaft parts are a common type of mechanical parts production.
2 – Box parts
The complex structure of box parts usually requires multi-surface machining and hole system machining. During the machining process, the parallelism and perpendicularity of each surface and the positional accuracy of the holes need to be ensured.
3 – Mold parts
The shape of the mold parts is often special, which requires special processing means such as EDM and WEDM in order to meet the requirements of its complex shape and high precision.
4 – Thin-walled parts
Thin-walled parts are prone to deformation during machining and require special clamping methods and cutting processes to minimize deformation. The machining of thin-walled parts is one of the challenges in the production of machine parts.
5 – High precision parts
The machining of high-precision parts is a high-end area in the production of mechanical parts.
High-precision parts need to be processed in a constant-temperature environment to minimize the impact of temperature changes on the accuracy of the parts. Meanwhile, high-precision measuring equipment is used for inspection to ensure that the dimensional and form accuracy of the parts meet the requirements.
7 、Conclusion
Mechanical parts production is a key aspect of engineering and manufacturing, covering a wide range of areas from pre-production to machining processes, quality testing and equipment selection. Understanding and mastering these aspects is essential to ensure the production of mechanical parts.