What are the most common types of surface treatments for metal parts?
In the intricate world of manufacturing, the performance, longevity, and appearance of metal parts often hinge on one crucial factor: surface treatment. At SCZY LTD, we’ve spent years perfecting these techniques, helping countless clients across industries unlock the full potential of their metal components. In this comprehensive guide, we’ll dive deep into the most common types of surface treatments, exploring how they work, their unique advantages and limitations, and real – world applications.
1. What is surface treatment?
Surface treatment refers to a broad range of processes designed to alter the properties of a metal’s outer layer. It’s not just a finishing touch; it’s a strategic approach to enhance durability, improve functionality, and elevate aesthetics. Whether it’s protecting against corrosion, increasing hardness, or creating a visually appealing finish, surface treatments can transform a basic metal part into a high – performance, market – ready product.
At SCZY LTD, we understand that each project has unique requirements. That’s why we offer a customized approach to surface treatment, carefully selecting the most suitable process based on the metal type, application, and desired outcome.
2. What are the different types of surface treatments?
The world of surface treatment is diverse, with numerous techniques available to meet different needs. Some focus on protection, while others prioritize appearance or performance. Here, we’ll explore the most common types, from tried – and – true methods to innovative solutions.
3. Anodizing: The Go – To for Aluminum Parts
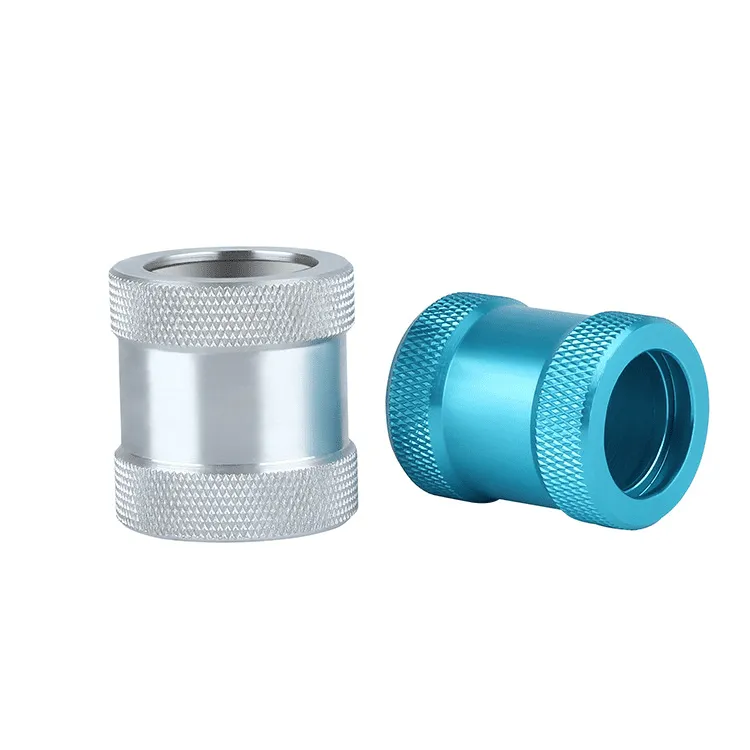
turning-parts-1
How Anodizing Works
Anodizing is a electrochemical process that creates a durable oxide layer on the surface of aluminum and its alloys. This layer is not only thicker than the natural oxide film but also highly porous, allowing for easy colorization and customization.
Creating a Durable Oxide Layer: During anodizing, the aluminum part is immersed in an electrolyte solution and subjected to an electric current. This causes oxygen ions to react with the aluminum surface, forming a tightly – bonded oxide layer. The thickness of the layer can be precisely controlled, ranging from a few microns for decorative purposes to over 25 microns for heavy – duty applications.
Colorization and Customization Options: One of the key advantages of anodizing is its ability to accept a wide range of colors. Dyes can be added to the porous oxide layer, resulting in vibrant, long – lasting hues. From classic silver and black to bold blues and reds, anodizing offers endless possibilities for creating visually striking products.
Advantages & Limitations
Excellent Corrosion Resistance: The oxide layer created during anodizing provides excellent protection against corrosion, making it ideal for outdoor applications. For example, anodized aluminum patio furniture can withstand years of exposure to sun, rain, and humidity without rusting or fading.
Limited to Aluminum – Based Alloys: While anodizing is highly effective for aluminum, it cannot be applied to other metals. This limitation means that for projects involving steel, copper, or other materials, alternative surface treatment methods must be considered.
4. Plating: A Versatile Solution for Corrosion Resistance
Popular Plating Variations
Plating involves depositing a thin layer of another metal onto the surface of the base metal. This can be done through various methods, such as electroplating, electroless plating, and physical vapor deposition (PVD).
Zinc Plating for Sacrificial Protection: Zinc plating is one of the most common forms of plating, especially for steel components. Zinc is more reactive than steel, so when exposed to the elements, it corrodes preferentially, sacrificing itself to protect the underlying metal. This “sacrificial” protection makes zinc – plated parts highly resistant to rust and corrosion, making them suitable for applications like automotive fasteners and outdoor hardware.
Chrome Plating for Hardness and Shine: Chrome plating not only provides a shiny, attractive finish but also increases the hardness and wear resistance of the metal surface. It’s commonly used in the automotive industry for decorative trim, as well as in machinery components that require high – wear resistance, such as piston rings.
Cost vs. Performance
Precious Metal Plating Trade – Offs: Plating with precious metals like gold or silver can add a touch of luxury and enhance electrical conductivity, but it comes at a high cost. These types of plating are typically reserved for high – end products, such as jewelry, electronics, and luxury automotive components.
Long – Term Durability Benefits: While the initial cost of plating can be higher compared to some other surface treatments, the long – term durability and performance benefits often justify the investment. A well – plated part can last significantly longer than an untreated one, reducing the need for frequent replacements and maintenance.
5. Powder Coating: Combining Aesthetics and Durability
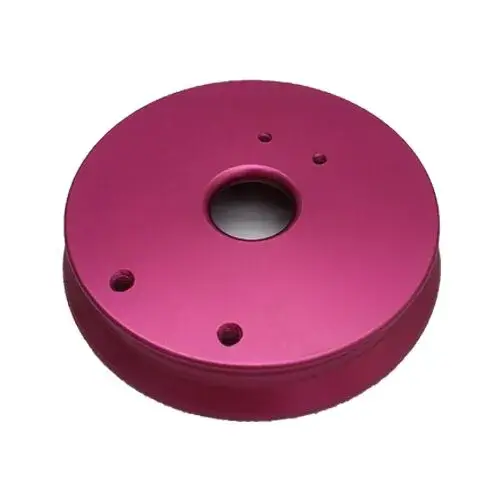
Powder coating – parts
The Coating Process Explained
Powder coating is a dry finishing process that involves applying a fine powder to the metal surface, which is then cured under heat to form a hard, durable coating.
Dry Powder Application & Curing: The powder is electrostatically charged and sprayed onto the metal part, causing it to adhere evenly. The part is then placed in an oven, where the heat causes the powder to melt, flow, and chemically bond to the surface, creating a smooth, uniform coating.
Texture and Color Flexibility: Powder coating offers a wide range of colors and textures, from smooth, glossy finishes to textured, matte looks. This makes it a popular choice for both consumer products, like appliances and furniture, and industrial equipment, where durability and visual appeal are both important.
Real – World Applications
Consumer Products vs. Industrial Equipment: In the consumer market, powder – coated products stand out for their vibrant colors and scratch – resistant surfaces. For example, powder – coated bicycles not only look great but can also withstand the rigors of daily use. In the industrial sector, powder – coated equipment is more resistant to chemicals, abrasion, and UV damage, extending its lifespan and reducing maintenance costs.
Resistance to Scratches and UV Damage: Unlike traditional paint, powder coating forms a tough, resilient layer that is highly resistant to scratches, chips, and fading caused by sunlight. This makes it an ideal choice for outdoor applications, such as street signs and outdoor lighting fixtures.
6. Painting: Traditional yet Effective for Visual Appeal
Liquid Paint Techniques
Painting is one of the oldest and most widely used surface treatment methods, involving the application of liquid paint to the metal surface.
Spray Painting for Uniform Coverage: Spray painting is a fast and efficient way to apply paint evenly over large surfaces. It’s commonly used in automotive manufacturing, where robots apply multiple layers of paint to achieve a smooth, high – quality finish.
Brushing for Detailed Finishes: For smaller parts or areas that require more precision, brushing can be used. This method allows for greater control over the paint application, making it suitable for intricate designs or touch – ups.
Maintenance Challenges
Prone to Chipping and Fading: While paint can provide a beautiful finish, it is more prone to chipping, peeling, and fading compared to other surface treatments. Exposure to sunlight, moisture, and physical abrasion can cause the paint to deteriorate over time, requiring regular touch – ups or repainting.
Cost – Effective for Small – Scale Projects: Despite its limitations, painting can be a cost – effective option for small – scale projects or when a quick, temporary finish is needed. It also offers a high degree of design flexibility, allowing for custom colors, patterns, and finishes.
7. Electropolishing: Achieving a Mirror – Like Finish
Chemical Polishing Process
Electropolishing is an electrochemical process that removes a thin layer of metal from the surface, resulting in a smooth, mirror – like finish.
Removing Surface Imperfections: During electropolishing, the metal part is immersed in an electrolyte solution and connected to an electrical circuit. The electric current causes the peaks and valleys on the metal surface to dissolve at different rates, gradually smoothing out the surface and removing scratches, burrs, and other imperfections.
Enhancing Hygiene in Medical Equipment: The smooth, seamless finish achieved through electropolishing is not only aesthetically pleasing but also easier to clean and sterilize. This makes it a preferred surface treatment for medical equipment, such as surgical instruments and implants, where hygiene is of utmost importance.
Performance Upgrades
Reducing Friction and Wear: By eliminating surface irregularities, electropolishing reduces friction between moving parts, improving their efficiency and reducing wear. This is particularly beneficial for components in machinery, such as bearings and gears.
Improved Corrosion Resistance: The smooth surface created by electropolishing is less likely to trap moisture and contaminants, reducing the risk of corrosion. This can extend the lifespan of metal parts, especially in harsh environments.
8. Sandblasting: Preparing Surfaces and Creating Textures
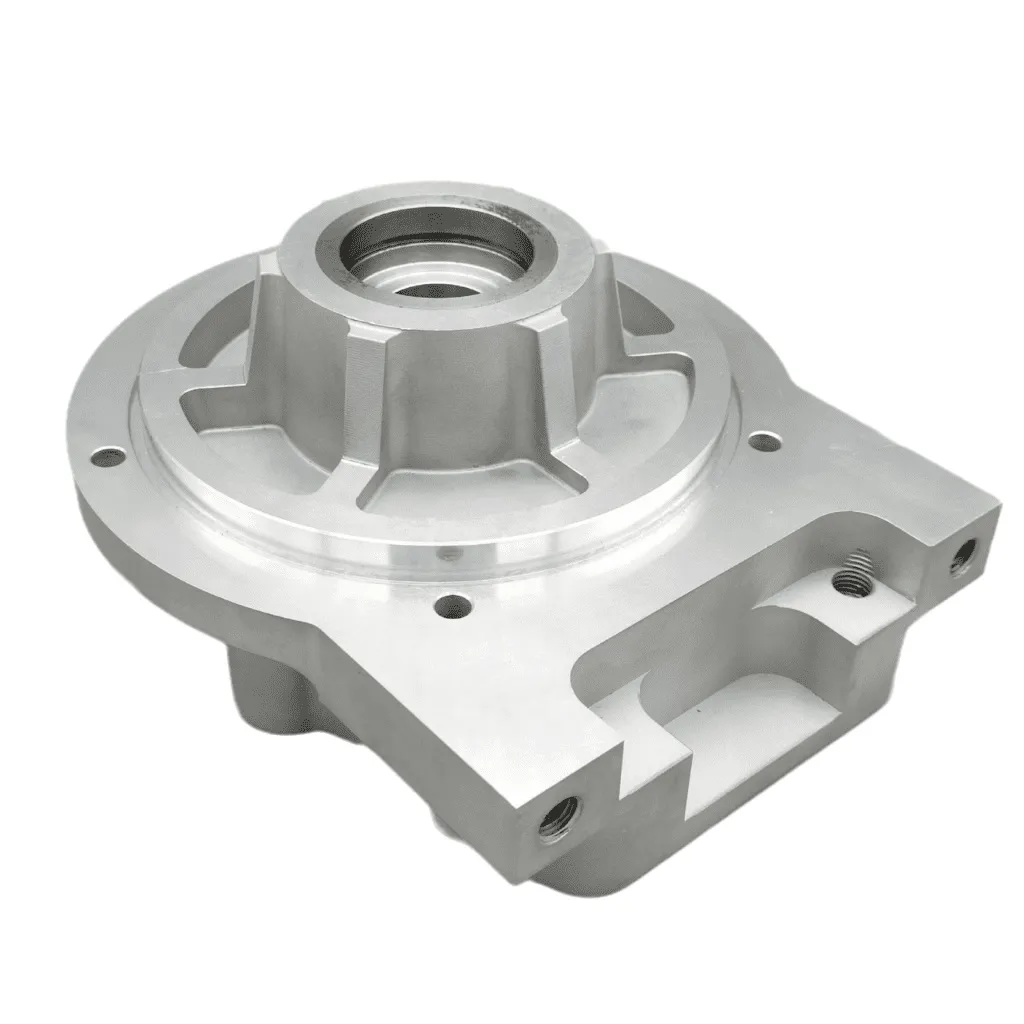
CNC-Machined-Parts-1-1024×1024
Blasting Media Options
Sandblasting involves propelling abrasive particles at high speed onto the metal surface to clean, etch, or texture it.
Aluminum Oxide for Aggressive Etching: Aluminum oxide is a hard, durable abrasive that is ideal for aggressive surface preparation. It can quickly remove rust, paint, and other contaminants from metal surfaces, as well as create a rough texture that improves the adhesion of subsequent coatings.
Glass Beads for Subtle Textures: For a more delicate touch, glass beads can be used. These create a smooth, satin – like texture on the metal surface, making it suitable for decorative applications or for preparing surfaces that require a less aggressive treatment.
Dual – Purpose Applications
Surface Cleaning Before Coating: Sandblasting is often used as a preparatory step before applying other surface treatments, such as painting or powder coating. By removing contaminants and creating a rough surface, it helps ensure better adhesion of the coating, resulting in a more durable and long – lasting finish.
Aesthetic Appeal in Design Projects: In addition to its practical uses, sandblasting can also be used to create unique textures and patterns on metal surfaces. This makes it a popular choice in architectural and design projects, where the texture of the metal can add visual interest and character.
9. Heat Treatment: Enhancing Metal Properties from Within
Types of Heat Treatment
Heat treatment involves heating and cooling the metal in a controlled manner to change its internal structure and properties.
Annealing for Softening and Stress Relief: Annealing is a process that involves heating the metal to a specific temperature, holding it at that temperature for a period of time, and then slowly cooling it. This softens the metal, reduces internal stresses, and improves its ductility, making it easier to shape and form.
Tempering for Balanced Hardness: Tempering is often used after hardening to reduce the brittleness of the metal while maintaining its hardness. It involves heating the metal to a lower temperature than hardening and then cooling it quickly, resulting in a more balanced and durable material.
Industrial Use Cases
Strengthening Tool Steel for Machining: In the manufacturing of cutting tools, heat treatment is crucial for achieving the right balance of hardness and toughness. By hardening and tempering tool steel, it becomes more resistant to wear and can maintain its sharp edge for longer periods, improving the efficiency of machining operations.
Improving Ductility in Aerospace Alloys: Aerospace components need to be strong yet lightweight. Heat treatment processes can be used to enhance the ductility of alloys, allowing them to withstand the stresses of flight while reducing weight, which is critical for fuel efficiency.
10. Chemical Conversion Coatings: Thin but Mighty Protectors
Common Coating Varieties
Chemical conversion coatings are thin, invisible films that form on the metal surface through a chemical reaction.
Zinc Phosphate for Primer Adhesion: Zinc phosphate coatings are often used as a primer before painting or powder coating. They create a rough, porous surface that improves the adhesion of the topcoat, ensuring a more durable and long – lasting finish.
Chromate Conversion for Corrosion Barriers: Chromate conversion coatings provide excellent corrosion resistance, especially for aluminum and magnesium alloys. They form a thin, self – healing film that can protect the metal from moisture and other corrosive elements.
Microscopic Advantages
Non – Thickening, Preserving Part Dimensions: Unlike some other surface treatments, chemical conversion coatings are extremely thin, typically only a few microns thick. This means they do not significantly increase the size or weight of the part, making them ideal for applications where dimensional accuracy is critical.
Ideal for Complex Geometries: The chemical reaction that forms these coatings occurs uniformly across the metal surface, regardless of its shape or complexity. This makes chemical conversion coatings suitable for parts with intricate designs or hard – to – reach areas.
11. Surface Treatment Case Studies
Case Study 1: Outdoor Furniture for a Luxury Resort
A luxury resort approached SCZY LTD with a need for durable, stylish outdoor furniture. We recommended anodizing for the aluminum frames, which not only provided excellent corrosion resistance but also allowed for custom color matching to the resort’s aesthetic. The powder – coated aluminum tabletops added a touch of elegance and were highly resistant to scratches and UV damage. The result? Furniture that has withstood the test of time and harsh coastal conditions, while maintaining its beautiful appearance.
Case Study 2: High – Precision Medical Instruments
For a medical device manufacturer, precision and hygiene were top priorities. We used electropolishing to create a smooth, mirror – like finish on the surgical instruments, reducing the risk of bacteria buildup and making them easier to clean and sterilize. The chemical conversion coating provided an additional layer of corrosion protection, ensuring the instruments remained in optimal condition throughout their lifespan.
12. FAQ
Q: How do I choose the right surface treatment for my project?
A: The choice of surface treatment depends on several factors, including the type of metal, the application, the desired appearance, and the budget. At SCZY LTD, our experts can help you evaluate these factors and recommend the most suitable treatment for your specific needs. We also offer sample testing to ensure the treatment meets your expectations.
Q: Can surface treatments be combined?
A: Yes, in many cases, surface treatments can be combined to achieve multiple benefits. For example, a part might be sandblasted first to prepare the surface, followed by powder coating for durability and aesthetics. Our team at SCZY LTD has extensive experience in combining different treatments to create customized solutions for our clients.
Q: How long does a surface treatment last?
A: The lifespan of a surface treatment varies depending on the type of treatment, the environment it is exposed to, and the level of wear and tear. Some treatments, like powder coating and anodizing, can last for many years, while others, such as paint, may require more frequent maintenance or reapplication. At SCZY LTD, we provide detailed information on the expected durability of each treatment based on our experience and industry standards.
13. In collaboration with sczyltd
At SCZY LTD, we pride ourselves on being a leading provider of surface treatment solutions. Our team of experienced engineers, technicians, and designers is dedicated to delivering high – quality results that meet and exceed our clients’ expectations. Whether you’re working on a small – scale project or a large – scale production run, we have the expertise, equipment, and resources to handle it.
We offer a full range of surface treatment services, from anodizing and plating to powder coating and heat treatment. Our state – of – the – art facilities are equipped with the latest technology and equipment, ensuring precision, consistency, and efficiency in every project.
But our commitment doesn’t end with the treatment process. We also provide comprehensive support, including technical advice, sample testing, and quality control. Our goal is to build long – term partnerships with our clients, helping them succeed in their industries by providing the best possible surface treatment solutions.
If you’re looking for a reliable, experienced partner for your surface treatment needs, look no further than SCZY LTD. Contact us today to discuss your project and find out how we can help you bring your metal parts to life.